Welcome to our fresh guide on how to conduct an industrial energy audit in your factory. In this post, we explain the process in simple, practical steps so you can spot wasted energy, improve efficiency, and cut costs. We cover everything from preparing for the audit to gathering data on-site, analyzing that data, and implementing improvements. You will also learn how Industrial Energy Audit Services for Manufacturing Plants like those offered by Daitan Solution can support you in creating a more energy-smart facility. Let’s dive in and transform your factory into a model of efficiency.
Understanding Industrial Energy Audits in a Factory
An industrial energy audit is essentially a health checkup for your factory. It involves a thorough review of how energy flows through your facility and identifies where improvements can be made. Unlike audits for offices or residential spaces, industrial audits face unique challenges. In a factory setting, heavy machinery, continuous production lines, and specialized equipment mean that energy use is complex and often difficult to track.
The primary goal of an industrial energy audit is to pinpoint areas where energy is wasted and to recommend simple changes that lead to big savings. This process not only helps in reducing your energy bills but also improves the reliability of your machines and the overall production process.
Factory-Specific Challenges and Equipment
Factories have their own set of challenges when it comes to energy use. Here are a few common issues that make industrial audits both essential and unique:
- Heavy Machinery and Continuous Production: Factories operate around the clock, and equipment often runs non-stop. This continuous operation can lead to energy waste if machines are outdated or not properly maintained.
- Complex Systems: A factory is not just one space. It includes production lines, storage areas, loading docks, and administrative offices. Each area may use energy differently, making it necessary to tailor the audit to each specific zone.
- Safety and Operational Constraints: Factories must maintain strict safety standards, and any audit must work around these without disrupting production. This means scheduling inspections during off-peak hours or in phases.
- High Energy Consumption: With large-scale operations, even small inefficiencies can result in significant energy loss and higher costs.
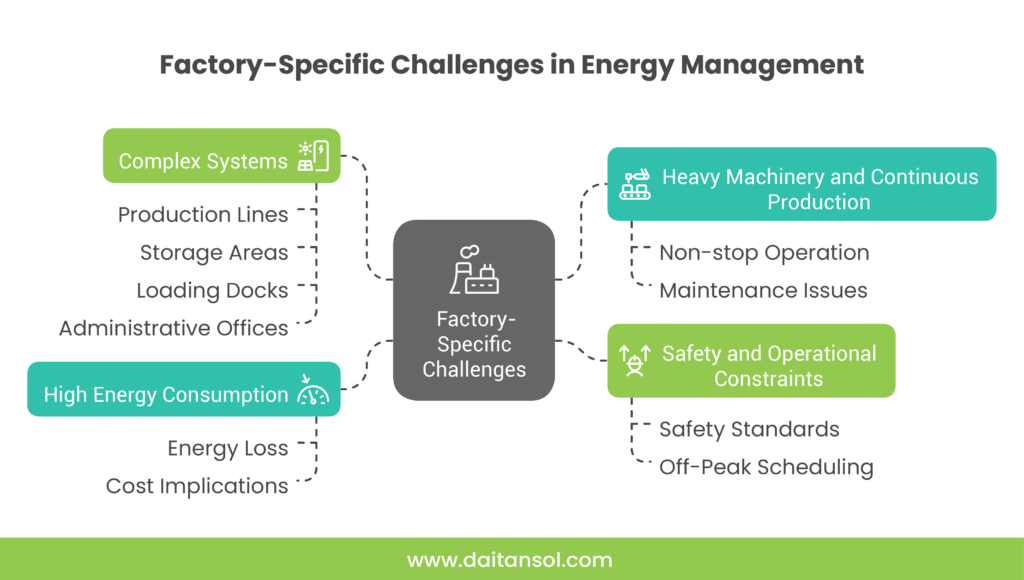
Addressing these challenges requires a customized approach to the audit, ensuring that every part of the factory is evaluated accurately.
Preparing for the Energy Audit
Preparation is the cornerstone of a successful energy audit. Before you bring in external experts or start the process, here are the key steps you should take:
Gather Your Energy Data
Collect all historical energy records such as utility bills, energy consumption logs, and maintenance records. This data provides a baseline against which you can measure improvements after the audit.
Define Your Goals
Determine what you want to achieve with the audit. Are you looking to lower energy costs, reduce downtime, or increase the lifespan of your equipment? Setting clear goals helps focus the audit on the areas that matter most to your operation.
Identify Key Areas
Make a list of the sections in your factory that consume the most energy. Consider production lines, heating and cooling systems, and lighting. Knowing which areas to focus on will streamline the inspection process.
Involve Your Team
Inform your staff about the audit and ask them to note any concerns or inefficiencies they observe in their daily operations. Their input can be invaluable and may highlight issues that are not obvious in the data alone.
Daitan Solution can assist you during the preparation phase. Their experts in Industrial Energy Audit Services for Manufacturing Plants can help you gather and organize all necessary data and set realistic, achievable goals.
The On-Site Inspection Process
The on-site inspection is where the audit comes to life. This is the hands-on stage where experts walk through your factory and use specialized tools to identify inefficiencies.
Conduct a Detailed Walk-Through
A thorough tour of your facility is essential. Experts will examine every part of your factory, from the production floor to the loading docks and even administrative areas. They look for obvious signs of energy waste such as poorly maintained equipment, inefficient lighting, or areas with weak insulation.
Use Specialized Tools
During the inspection, auditors use modern tools that can capture precise energy data. For example, energy sensors can measure consumption levels, and thermal imaging cameras can detect areas where heat is lost. Data loggers might be installed to track energy use over time, giving you a complete picture of your factory’s energy profile.
Record Every Detail
No observation is too small. All findings are documented meticulously. This includes measurements, photos, and notes about potential energy-saving opportunities. The more detailed the information, the easier it will be to identify critical issues later.
Daitan Solution’s team excels in carrying out these detailed inspections. Their expertise ensures that every nook and cranny of your factory is evaluated, leaving no energy leak unnoticed.
Analyzing the Data and Creating Your Report
Once the on-site inspection is complete, the next step is to analyze the collected data and compile it into a clear, actionable report.
Analyze the Data
Review all the gathered information to identify patterns and pinpoint areas where energy is being wasted. Look for trends such as peak usage times, inefficient machinery, or parts of the building with excessive heat loss. Comparing your data against industry benchmarks can highlight where your factory stands.
Identify Key Issues
The analysis should clearly show which issues are having the most impact on your energy consumption. This might include machinery that consumes more energy than necessary, inefficient production processes, or outdated HVAC systems. Prioritize these issues based on their potential for savings and ease of improvement.
Create a Clear Report
Your audit report should be written in plain language, making it easy for everyone in your team to understand. Include visual aids like charts and graphs to illustrate key points. The report should cover:
- A summary of the audit process.
- Detailed findings with specific data points.
- A list of recommendations for improvements.
- Estimates of potential energy savings and return on investment.
With the help of Industrial Energy Audit Services for Manufacturing Plants, such as those provided by Daitan Solution, you receive a report that serves as a practical roadmap. The report translates technical data into actionable steps that you can implement immediately.
Implementing Recommendations and Ongoing Monitoring
The audit report is not just a document; it is a guide to making your factory more energy efficient. The next step is to put those recommendations into action.
Develop an Action Plan
Work with your team to create a detailed plan for implementing the recommendations. This plan should include:
- Specific tasks and responsibilities.
- A timeline for completing each improvement.
- A budget for any necessary upgrades or repairs.
Execute the Plan
Start with the recommendations that offer the greatest benefits for the least cost. For example, updating outdated lighting or optimizing HVAC settings can often be done quickly and lead to immediate savings.
Monitor Your Progress
After implementing changes, it is essential to monitor the results. Set up regular follow-up audits or continuous monitoring systems to ensure that the improvements are working as expected. This ongoing process helps catch any new issues early and keeps your factory running efficiently.
Daitan Solution supports you throughout this process. Their expertise in Industrial Energy Audit Services for Manufacturing Plants means they can help you not only plan and implement improvements but also set up systems for continuous monitoring.
Essential Tools and Techniques for a Successful Audit
Having the right tools makes the audit process much more effective. Here are some of the key technologies used in industrial energy audits:
Energy Sensors
Smart energy sensors measure the consumption of various machines and areas within your factory. These devices provide precise data on where energy is being used inefficiently.
Thermal Imaging Cameras
These cameras detect heat loss and pinpoint areas with poor insulation or overheating equipment. They are especially useful in large factories where it might be difficult to spot these issues with the naked eye.
Data Loggers
Data loggers collect energy usage data over an extended period. This information helps identify patterns and trends, allowing you to target specific areas for improvement.
Energy Management Software
Advanced software platforms analyze energy data in real time. They provide dashboards and alerts when energy consumption exceeds set thresholds, enabling quick intervention.
By using these tools, Industrial Energy Audit Services for Manufacturing Plants can deliver a detailed and accurate analysis of your factory’s energy use. Daitan Solution leverages these advanced technologies to ensure every inefficiency is identified and addressed.
Common Challenges and Practical Tips
Even with a well-planned audit, you may face some challenges. Here are common issues and tips to overcome them:
Incomplete Data
Sometimes, historical energy data may be missing or incomplete.
Tip: Start collecting energy data well in advance and maintain organized records.
Scheduling Conflicts
Factory operations often run continuously, making it hard to schedule an audit without interrupting production.
Tip: Plan the audit during off-peak hours or in phases to minimize disruption.
Technical Complexities
Industrial systems can be complicated, with multiple factors affecting energy use.
Tip: Work with experienced auditors who understand the unique challenges of industrial environments.
Resistance from Staff
Employees might be hesitant about changes or extra responsibilities during the audit process.
Tip: Communicate the benefits clearly and involve your team early on. Their insights can be crucial for a successful audit.
By anticipating these challenges and taking practical steps, you can ensure that your audit runs smoothly and leads to meaningful improvements.
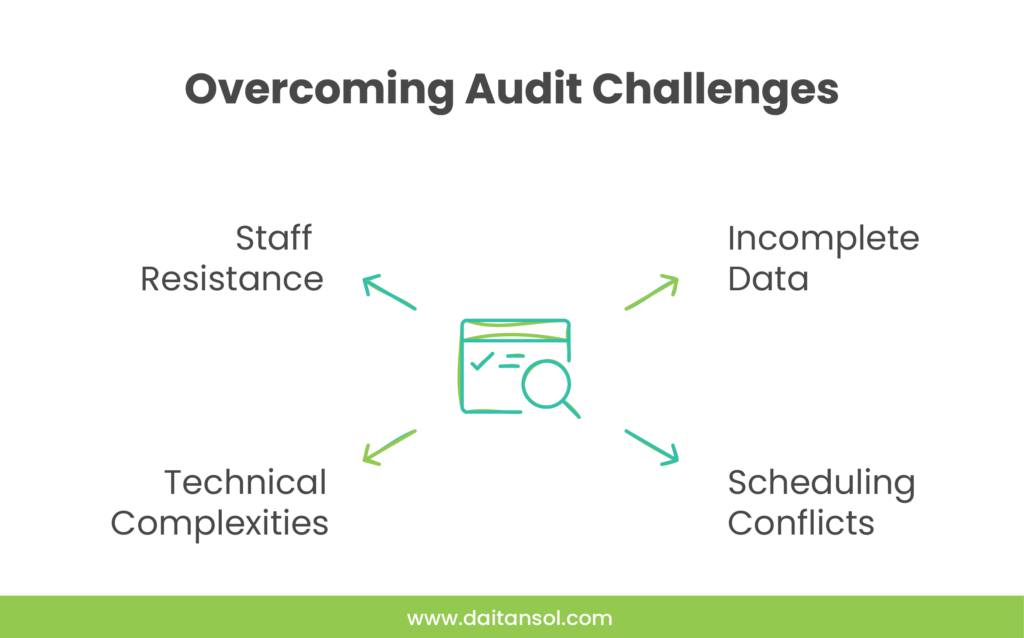
Future Trends in Industrial Energy Audits
The field of industrial energy audits is constantly evolving. Here are some trends that are shaping the future:
Increased Use of Real-Time Monitoring
The trend toward real-time monitoring is growing, with sensors and smart devices providing continuous data. This allows for quicker detection of inefficiencies and immediate corrective actions.
Integration of Artificial Intelligence
AI-powered analytics are becoming more common, helping to predict energy waste before it becomes a major issue. This proactive approach can lead to even greater savings.
Focus on Renewable Energy
As more factories incorporate renewable energy sources like solar or wind, audits are also focusing on how to optimize these systems. Improved energy management strategies can help blend traditional and renewable energy sources seamlessly.
Enhanced Data Analytics
With better software tools, data analysis is becoming more precise. Future audits will likely offer even more detailed insights and recommendations, making it easier to achieve your energy goals.
Daitan Solution stays on top of these trends by continually updating its methods and tools. Their commitment to excellence in Industrial Energy Audit Services for Manufacturing Plants means you benefit from the latest advancements in energy management.
Here are some common questions that factory managers often ask about industrial energy audits:
Q: How do I book an energy audit for my factory with Daitan Solution?
A: It’s easy. Visit our website or call our support team to schedule your consultation. Our experts are ready to help.
Q: What does an industrial energy audit cover?
A: An audit covers every aspect of your factory’s energy use, from machinery and lighting to HVAC systems and production processes. No area is left unchecked.
Q: How long does an industrial energy audit take?
A: The time required depends on your facility’s size. Most audits take a few days, and you will receive a detailed report shortly after the inspection.
Q: Can an energy audit really save me money?
A: Yes. By identifying where energy is wasted and offering clear recommendations, an audit can significantly lower your energy bills and improve your equipment’s performance.
Q: Why should I choose Daitan Solution for my energy audit?
A: Daitan Solution has years of experience, uses the latest tools, and provides actionable insights. Their expertise in Industrial Energy Audit Services for Manufacturing Plants ensures you get the best results.
Conclusion
Conducting an industrial energy audit in your factory is a smart move towards a more efficient and cost-effective operation. By following the steps in this guide from preparation and on-site inspections to data analysis and implementation you can uncover hidden energy waste and take meaningful action to save money and boost performance.
Partnering with experts like Daitan Solution can make all the difference. Their comprehensive Industrial Energy Audit Services for Manufacturing Plants are designed to guide you through every step of the process, ensuring that you get clear, actionable insights and lasting results.
Ready to improve your factory’s energy efficiency? Contact Daitan Solution today and schedule your energy audit. Let’s work together to build a smarter, more sustainable future for your operations.
By taking these steps and using the right tools, you are not just investing in an audit you are investing in the future of your factory. With expert guidance, clear data, and practical recommendations, you can unlock your facility’s full potential and enjoy significant savings. Start your journey to a more efficient and eco-friendly operation today.